To get a grasp of the monumental
changes that were
brought by the engineer
design of Komori’s new
Lithrone platform in 1981,
you must look back to 1965 and a company
known as Planeta, in the former
East Germany. Planeta was also rather
isolated, locked behind The Iron Curtain,
but the press maker had some brilliant
ideas. Few in the rest of West Germany
and Europe paid much attention when
Planeta launched its Variant press platform,
but Komori certainly did.
The Japanese press maker quickly saw the
benefits of the double-size impression
and transfer cylinders on the Variant. Although
the Kosmo was a unitized press,
the Kony was a bit of a discombobulation
of upper and lower unitized units. Komori
saw the light and embraced the
Planeta Variant’s forward-thinking unitized
double-size cylinder design. Planeta
is now a part of Koenig & Bauer.
Not everything Planeta was borrowed.
Komori retained the upper swing arm
first used on Miehles, then Rolands, and
made its own version of the Mabeg feeder
head and essentially improved or re-engineered
every part of the Planeta design
principles with a press that remains today
as a watershed beacon of Komori engineering
achievement. And it was fast. At
13,000 iph, the Lithrone eclipsed both
Roland and Heidelberg by 3,000 iph in
1981. I could go on and on about various
features but suffice to say the Lithrone
made Komori what it is today. Twentysix-,
28-, 44- and 50-inch Lithrones
would soon enter production.
During the early 1980s, the packaging
industry soon discovered the benefits of
using aqueous coatings instead of varnishes.
Komori became the first to build
a factory tower coater. True – Planeta had
done so earlier but these were simply
printing units less the inker. Komori
fashioned its own three-roll coating apparatus
and followed Planeta’s lead by
offering extended deliveries. Unless you
ordered a hollow transfer Lithrone, however,
running short-grain carton was not
ideal. Both the solid and skeleton, or
hollow cylinder, still only allowed substrates
of up to .032 inches (0.8 mm).
Roland and Heidelberg (1986) already
eclipsed this and of course Planeta had
the widest range up to 1.4mm or over .050
inches. This is why even today Koenig &
Bauer still carries the reputation as the
ultimate carton press. In 2017, when
every manufacturer can essentially run
the same caliper of board (including
Komori), Planeta’s early penetration into
that market continues to pay dividends
for Koenig & Bauer.
Buoyed by its strong sales, especially
into the U.S. and Europe, Komori pushed
to acquire the Harris Graphics Corporation
in 1988. In fact, Komori had made
what it assumed to be a deal with the
principle owner AM International, and
even released a press statement confirming
the acquisition. At that time,
Harris web division was a leader in commercial
and insert printing web systems.
When the dust settled, however, Komori was trumped at the final hour by Heidelberger
Druckmaschinen. No doubt anger
sidelined Komori executives, but not for
long as Komori swooped in to buy the
small French specialist packaging narrow-
web manufacturer Chambon. In
retrospect, considering the depressing
state of the web-offset business today,
Komori may have been done a favour.
It’s In The Metal
Komori grasped another sales tool. When
Japanese exports took off in the early
1970s, the West handed out the moniker
of “Japanese Junk,” from early cars that
would rust away to machinery that would
break from poor foundry methods. There
were a lot of consumer products leaving
Japan that had only one saving grace –
price. This story is an old one and we have
seen it reappear again with China’s entry
onto the world stage. In short, made-in-
Japan in 1970 meant inferior goods at
very cheap prices. It’s incredible to consider
how this has changed in less than 50
years.
I don’t know about you, but I can go
for days without thinking about cast iron.
But to machine builders, it’s a very important
topic. Komori was well aware of
the uphill battle it faced trying to export
a machine that was about 80 percent cast
iron. In fact, just about every heavy machinery
exporter did too.
Nebiolo S.p.A. of Italy faced the same
backlash. With a tarnished reputation,
Nebiolo turned to Meehanite to prove to
the world their cast was as good as any. So
Komori did a smart thing. Komori’s
major castings come from a company
called Kasakura Metech Co. and Kasakura
became a certified Meehanite
foundry in 1981, although its roots go
back to 1919. Meehanite is a process to
increase the quality of grey castings. It
was developed back in the 1920s by the
Ross Meehan Foundry in Chattanooga,
Tennessee. Meehanite Corporation was
formed to, among other things, license
third parties to use the technology which
essentially increased the Perlite and removed
Ferrite from the cast, strengthening
it.
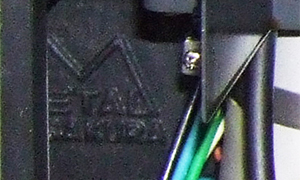
|
|
Heidelberg, which owns its own foundry,
already had a century of skill making
superior castings, but Komori’s supplier
was unknown outside Japan. Now, Komori
would emblazon their castings with
the famous “M” logo in bas relief to show
the world it could supply castings as
strong as anyone. Ironically, Mitsubishi
took a slightly different path when it did
the unthinkable by having a non-Japanese
company (Beiren of China), make much
of theirs. Kasakura now has a foundry in
China, too. |
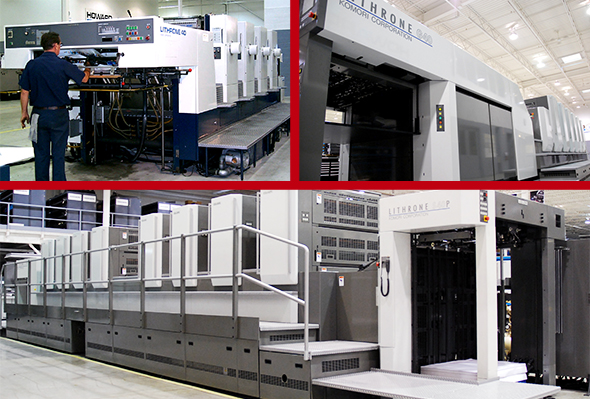 |
Top-left: Komori L40; Top-right: Komori GL40; Bottom: Komori LS40 |
No one today should question the superior
engineering of Komori presses.
After all the upheaval in the offset business,
Komori has remained the undisputed
leader in Japan and one of the
world’s top three press manufacturers in
the world. Quite a feat for a company that
always holds its cards close to the vest.
Like Heidelberg, KBA and Manroland,
Komori too finds the lithographic business
dwindling from the highs of the
1990s as digital devices take more and
more of offset’s position away.
Made in Japan and Israel
Landa Digital’s S10 press is already made
up of Komori transport, coating and
perfecting components. Komori signed
an agreement with Landa to both provide
traditional press components and also
exclusively market its own version of the
Landa S-10 as the Komori Impremia NS-
40. Since there is no way yet to determine
the success or failure of this platform, the
industry sits and ponders if these very
expensive Landa presses will be stars or
dogs. Knowing Komori, I’d put my
money on the former. However at
eye-watering prices even as a success
others will make that determination.
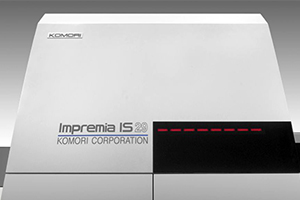 |
Konica Minolta also partnered with
Komori on the smaller Impremia IS29.
Komori even started selling its own guillotines
in 2014. I didn’t really think the
world needed another guillotine but... All
the while Komori keeps selling new generation
GL(X) 29- and 40-inch presses
and perfectors to a satisfied user group of
commercial printers. The crafty HUVdoped
UV, which uses much less power
and produces less heat, was a Komori-
Iwasaki-EYE invention that for a
brief few years had the market all to
themselves. Now, pretty much everyone
has a low-energy UV alternative to offer. |
Rarely first with new designs, Komori
researches the market well. If a competitor’s
leap is deemed important enough,
you will see it worked into a Komori press.
Just look at the up and over delivery from
Manroland, vacuum feeder from Roland
and Heidelberg, or even the Wallscreen
and Inpress concepts from Heidelberg.
They all made it into the Komori GL40 a
few years later. There is also a flat line
across all major press makers today as
everyone makes an outstanding press.
Few know the inner workings behind
the Japanese mystic, even fewer care.
Mitsubishi MHI’s recent exiting of its
sheetfed business, handing the keys to
Ryobi, has not done much to eliminate a
competitor. If, as many suspect, the Mitsubishi
Web program may be shuttered or
sold off entirely, the landscape may only
alter inches not feet.
There is a source of puzzlement when
benchmarking Made in Japan with the
rest of the world. Certainly exporters are
heavily supported by government incentives
(as well as periodic tax benefits for
the domestic market), and almost all
Japanese branch units run lean with very
low head counts. With such world-acclaimed
products, some find it ironic that
basic functions such as spare parts and
communication vary greatly from region
to region. The Germans remain leaders
with greater transparency in customer
relations. In short, to outsiders it seems
the only thing holding back Japanese
companies is in fact themselves.
When Toyota was named the world’s
largest car company in 2016, it might
have been a statement that some in the
automotive industry questioned. Not the
fact that Toyota was the largest and so
successful, but why it took them so long.
Virtually, every manufacturing segment
has a Japanese company ranked at
or near the top. Komori is no exception.
The new super factory/assembly hall
opened in 2003 in Tsukuba, Japan, was
years in the planning and built with the
next technology leap in mind.
KANDO, the new catchword meaning, as Komori
interprets: “Beyond Expectations... is an
expression of who Komori wants to be
and why it’s important to you.”
Every press manufacturer has a few
product embarrassments in their closets.
Some more than others. No one is exempt.
In Komori’s case they have been
rather fortunate in successfully dodging
major blunders over its 94 years. Not only
do they have a dedicated following but
their management team has taken great
pains to run a conservative, profitable
world-class company. |
|
The year 2018 marks Komori’s 95th
year in business and a very good reason to
celebrate a special company that from
1923 to now has been in the offset business
almost exclusively. You may not see
Komori race out in front of the pack in a
marathon, but you will sure see them at
the finish line.
|